Online Grocery Pick Up
The Boom of Online Grocery Pick Up
Even before the onset of the COVID-19 pandemic that necessitated the need for social distancing and associated modifications in how the public shops, the grocery store and supermarket industry was seeing a noticeable shift in consumer buying habits. Specifically, more and more shoppers had begun to do their buying online, rather than in-person. In fact, a report from the Food Marketing Institute indicated that upwards of 70% of Americans would do all their grocery shopping online by 2030, which would help make Online Grocery Pickup, or OGP, a $100 billion business.
This shift has been illustrated by the actions of a major national big-box retailer with a grocery offering, which recently created new, but distinct, upgrades at two of its sites in order to optimize their OGP offerings, with KPS Global, Inc., contributing its cold-storage unit design, engineering and equipment expertise to both.
Case 1: Implement An Online Grocery Solution With Limited Space
The Situation
The Response
As a solution, the retailer commissioned the creation of an entirely new robotic order-fulfillment system that would be supported by the existing work force. Specifically, a new 60-foot by 150-foot addition was built to house the incoming OGP order-fulfillment system.
As part of the new building, KPS Global designed and built a proprietary 100-foot long, 30-foot wide and 32-high cooler/freezer. The cooler-freezer had to be designed so that it could accommodate a rail system on which the order-picking robots would ride. The cooler/freezer also had to feature several small doors that would allow the robots to enter and exit it, while not allowing excess hot air to enter or cold air to escape.
Now in operation, the new OGP program has made the order-fulfillment system more efficient and error-free. An operation that used to require 30 people now only needs five, while the robotic system can accurately pick a family of four’s groceries in less than five minutes, a significant reduction from the 35-40 minutes it would previously take.
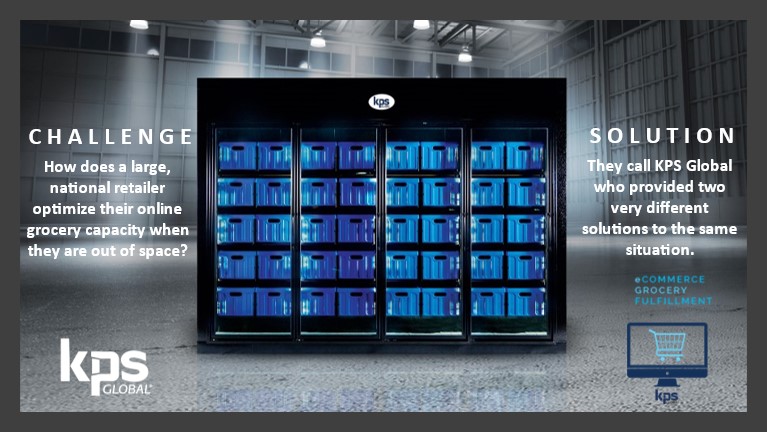
Case 2: Meet OGP Demand With Robotics
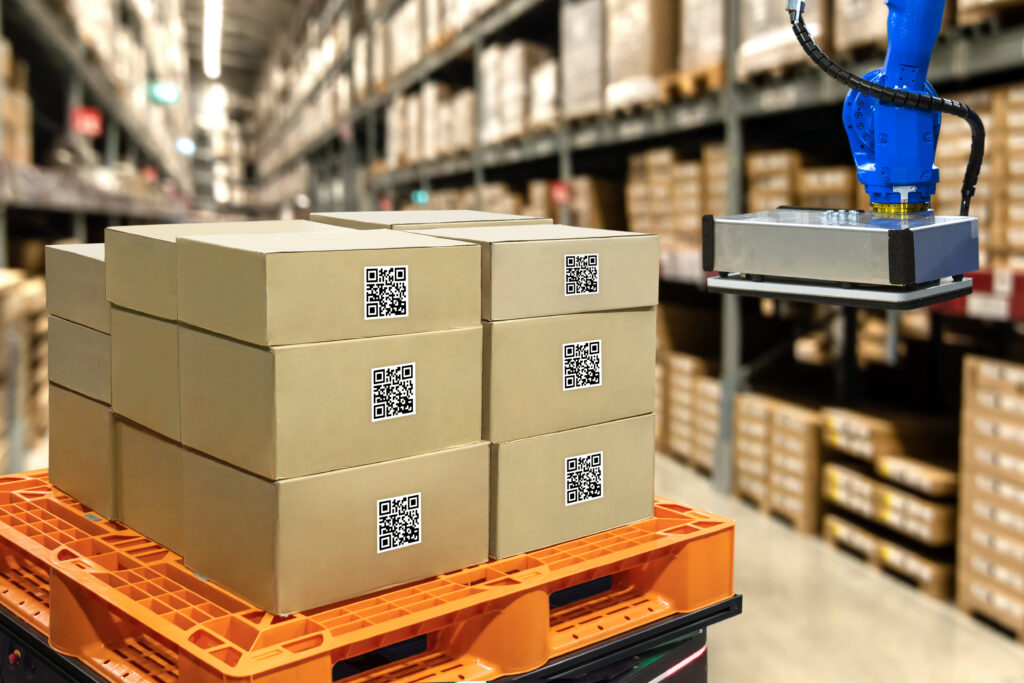
The Situation
The Response
With expansion of the current footprint not a viable option, a new modular building with an upgraded cooling system was constructed next to the existing structure. Working with the retailer from Day One, KPS Global designed a turnkey solution that meant the retailer needed to deal with just one source for the project. The KPS Global contribution included building the new annex; supplying and installing new coolers and freezers; installing all of the refrigeration lines; and installing a new air-conditioning system. The entire project took less than eight weeks to complete, with the quick construction schedule meaning minimal disruption to the existing OGP operation.
With the new annex now fully operational, the retailer has already reaped the benefits of a new dedicated OGP space that is more comfortable and easy to work in for the staff, with the modular building able to be expanded as demand for OGP services continues to grow.
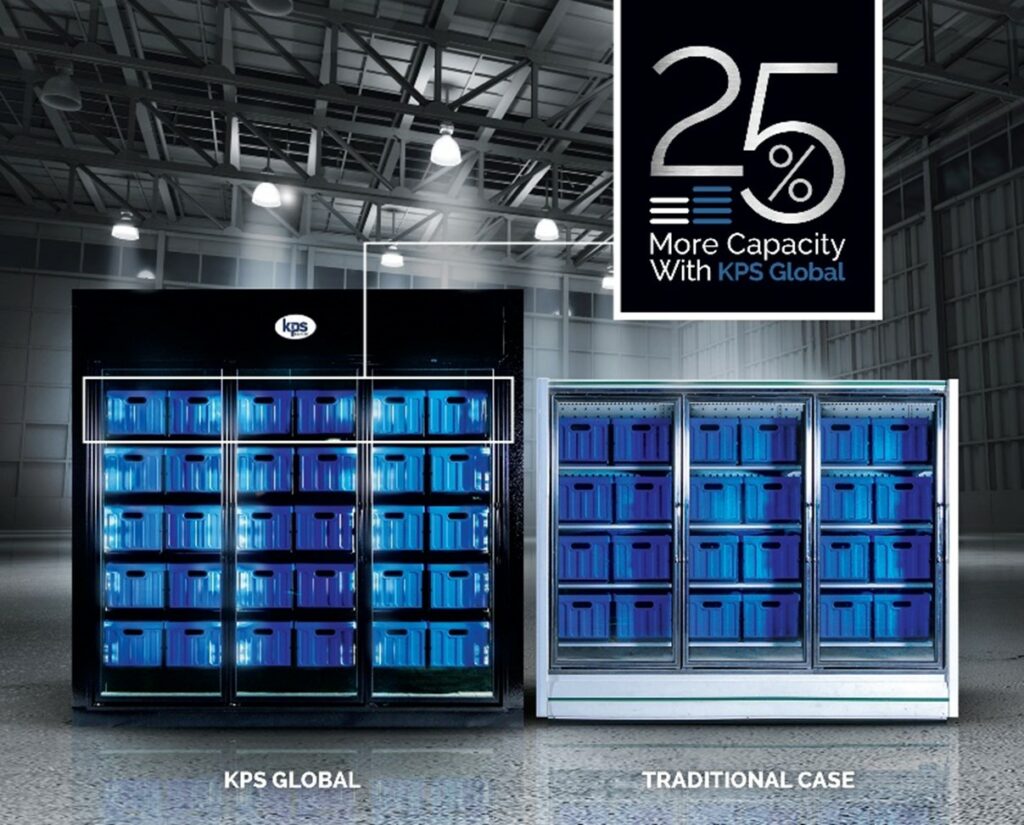