What is Expanded Polystyrene
Expanded polystyrene (EPS) is a durable, insulative, and lightweight foam that is highly versatile. Its development began in 1929 by IG Farben, and this research was built upon by Dow Chemical Co. in the 1930s
Since its creation, EPS has been vital to various industries, including shipping, automotive, and construction. EPS boasts a multitude of characteristics that make it ideal for these diverse applications. It is recyclable, waterproof, non-toxic, chemically inert, insoluble, and has long-term, stable, low thermal conductivity with an R-Value of R4.15 per inch at 55°F. Further, EPS is a durable, structurally-sound foam with a compressive strength of up to 60 psi.
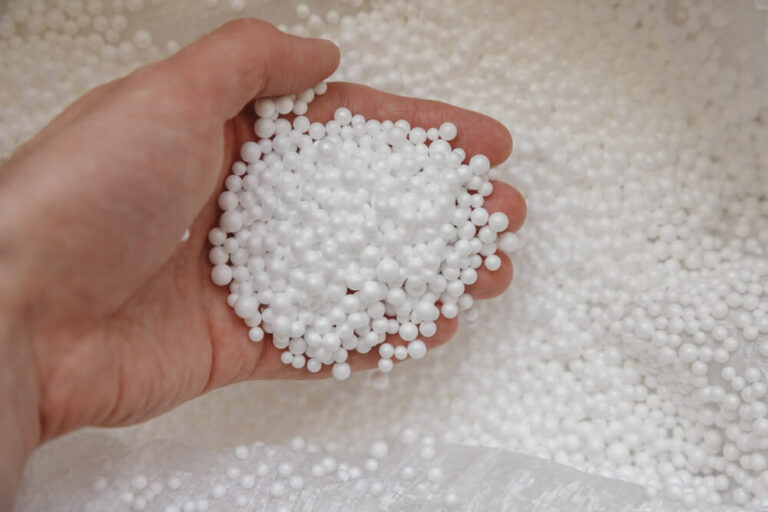
How is Expanded Polystyrene (EPS) Made?
EPS is manufactured using polystyrene, a colorless, hard thermoplastic – meaning that it softens when heated and hardens when cooled. Polystyrene starts as tiny plastic beads, which are derived from styrene monomer – an organic raw material. These beads are as small as a grain of sand at only about 1 millimeter in diameter. They are hollow and filled with a blowing gas, pentane.
But how do these tiny beads turn into EPS? The expanded polystyrene manufacturing process can be broken down into four distinct steps:
- Pre-expansion: Steam is used to pre-expand, or pre-foam, the polystyrene beads. This steam, typically around 392°F (200°C), causes the pentane gas to expand in the hollow chamber inside the bead and allows air to enter. This forces the beads to undergo their first expansion, where they will expand to 40 to 50 times their original size. This process is known as polymerization, and it gives EPS its insulative capabilities. Now, the beads are approximately 90% air.
- Maturing: Following their initial expansion, the beads are left to mature for 1-3 days, typically in large hanging bags. This step allows the material to cool. The pentane gas will liquefy, creating a partial vacuum inside of the bead.
- Molding: Once the partially expanded beads have cooled, they are poured into a large mold machine. This machine steam-fuses the beads together for 5-10 minutes. This steam prompts the beads’ final expansion – an additional 10% growth. The machine also molds the now larger beads into a solid block. The density of the final EPS block is determined by the quantity of beads in the final mold – it can range from about 0.75 to 3 lb/ft3. After the beads are molded, a vacuum removes any remaining water and the blocks are left to cure and cool, sometimes assisted by cool water running outside of the mold. This final product is about 98% air.
- Cutting: EPS is typically molded into massive blocks that can be cut into virtually any shape through a unique EPS foam-cutting process. These cuts are made using a heated nichrome wire, which vaporizes the EPS as it passes through to make the cleanest lines possible.
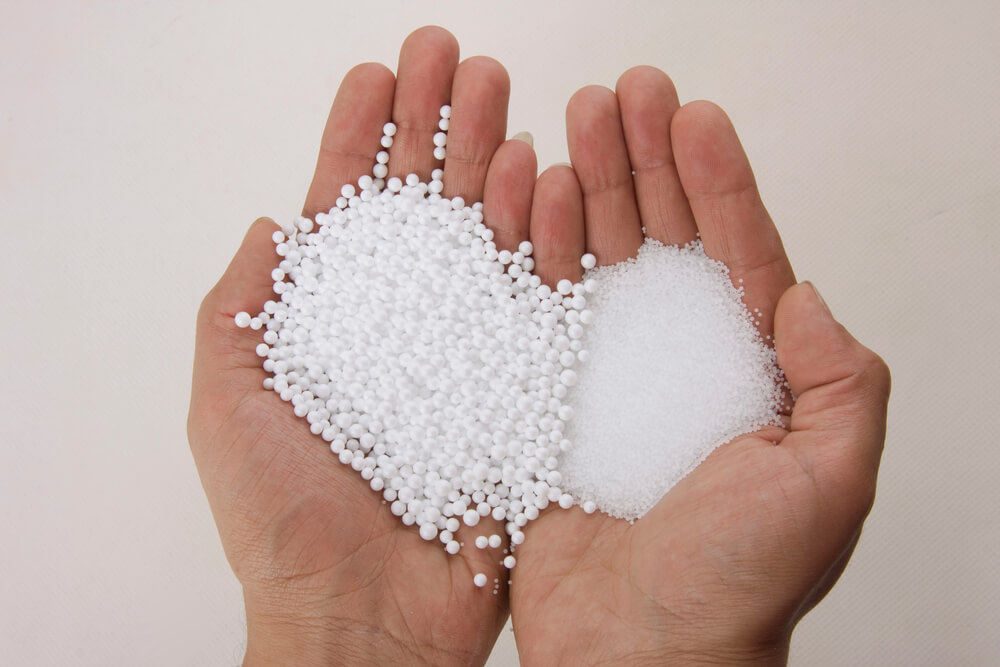
How Does KPS Global Use EPS for Wall Panels?
KPS Global uses expanded polystyrene as the core for insulated metal panels.
Insulated Metal Panels (IMPs) are insulated building panels made up of two steel skins sandwiching a core made from either EPS, polyurethane, or mineral wool. IMPs are commonly used for cold storage warehouses and other large-scale temperature-controlled environments.
At KPS Global, we sell “Continuous Line Panels” (CLP) to describe these EPS Insulated Panels.
Compared to other IMPs, EPS Insulated Metal Panels or Continuous Line Panels are cost-effective and can span longer distances – up to 30 feet on ceilings without structural support. This is due to the density and structural strength of the EPS foam. They also have shorter lead times and are easier to install for large-scale projects compared to traditional cam-lock panels due to the foam-to-foam, tongue, and groove joints.
Additionally, the frameless nature of CLP means a direct connection between the foam in each consecutive panel. This gives the joints of CLP structures a consistently high R-Value, decreasing the likelihood of thermal bridging at these typically vulnerable points. CLP can have an R-Value of R8 to R44 depending on thickness.
Customers can achieve their ideal R-Value and match their exact size specifications due to the customizable nature of this product – Continuous Line Panels are anywhere from 2-10 inches thick, 8-45 feet long, and 45 inches wide. With this, they can be used for many unique applications but are best suited for very large-scale interior applications like food processing facilities, distribution warehouses, clean rooms, and horticulture or “grow” rooms.
For more information about expanded polystyrene (EPS) applications for wall or ceiling panels in cold storage, contact the experts at KPS Global.